A pervasive problem in the cannabis industry is limited equipment durability. Specifically, in large-scale ethanol extraction, the centrifuge is the centrepiece and workhorse of the entire extraction process. Excessive wear and tear, due to the shear forces and workloads pushed onto these pieces of equipment, can lead to costly downtime and hard-to-find replacement of parts with long lead times. By pushing the limits of the EV-MASS ethanol centrifuge in the product development phase we identified several features that significantly reduce costly breakdowns and improve return on your investment.
It is important to first understand the reasons why many ethanol centrifuges are prone to failure. A specialized motor spins the drive shaft, which in turn spins the basket to remove residual ethanol out of the biomass. However, during an extraction batch, ethanol centrifuges can generate a massive amount of G-forces to pull the ethanol out of the biomass. This can produce G-forces equivalent to over 10,000lbs. This form of rotational force can cause significant vibrations throughout the equipment, leading to strain on the shaft and an unbalancing of the basket, causing even more strain which can lead to unpredictable maintenance if not mitigated during the extraction cycle. If the G-forces were not enough, the ideal process runs at -40C which can cause 304 steel under that load to become brittle. Therefore these cold temperatures will often weaken the steel of a 304 SS shaft, which can result in bending, causing increased vibrations and potentially critical failure.
Ethanol centrifuges need to run at peak efficiency to maximize the benefits for cannabis processors. However, the companies using this equipment should not be expected to push an ethanol centrifuge to a point of failure to understand its limits. For example, though many ethanol centrifuge companies claim their equipment can safely operate at -40 C, this is often the absolute limit and anything at or beyond this temperature can lead to catastrophic failure. To address this, Evolved Extraction Solutions conducted extensive testing, well beyond the limits of most centrifuges. This testing identified specific weaknesses that lead to premature equipment failure, resulting in costly downtime. By pushing our system beyond the stated limits, we assure that the optimal performance can be reached safely, ensuring maximum durability and extraction efficiency.
The EV-MASS Difference
Our EV-MASS ethanol centrifuge includes significant improvements to shaft strength and vibration mitigation. The shaft is made of Duplex 2205 Stainless Steel, coated with a thermal arc spray which is a corrosive resistant SS Alloy. Duplex 2205 SS is a family of SS that provides excellent ductility, improved resistance to corrosion and optimal mechanical strength. Pairing this with a thermal arc spray increases surface hardness to 68 HRC, allowing us to use a proprietary lip seal design rather than a traditional mechanical seal that has been known to cause degradation issues and increased maintenance. Furthermore, the duplex 2205 SS reduces the risk of shaft bending at sustained temperatures of -40 C.
To reduce vibrations while in the spin cycle we have developed a new Automated Vibration Management System (AVMS). The AVMS includes 3 key features:
Innovative Vibration Sensor
The system utilizes an intrinsically safe vibration sensor connected to the PLC to work as a feedback mechanism, allowing operators to maximize the RPM of the centrifuge to maintain the most efficient batch spin cycle.
Dampening Feet
Dampening feet reduce remaining minimal vibrations created at high RPM
Individually Calibrated Baskets
Each basket is calibrated to each unique system to a balancing quality grade of G6.3 which is the same precision as an aircraft gas turbine, limiting vibrations and increasing long-term durability.

Extraction Efficiency Graph
After the agitation cycle, the ethanol drains and the soaked biomass remains, and is at its heaviest. Therefore, at this point, the basket’s critical speed is at its lowest point. As the RPM increases and ethanol is removed from the biomass the weight of the biomass decreases which in turn increases the critical speed. The fact that the EV-MASS CS-30 can determine this automatically and in real-time ensures that the RPM is always operating in the optimal efficiency range depicted as the green line on the graph. The blue stepped line is a representation of a traditional centrifuge program maintaining an RPM too long, wasting time/money, and then raising too quickly causing premature wear and tear.
Learn why the EV-MASS Ethanol Extraction System is raising the bar for extraction companies who are pushing the limits of what ethanol extraction equipment can do. Contact us today!
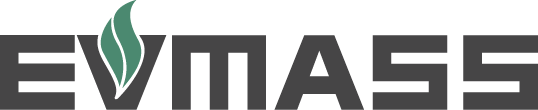